The International Standard Production Process of Export Furniture
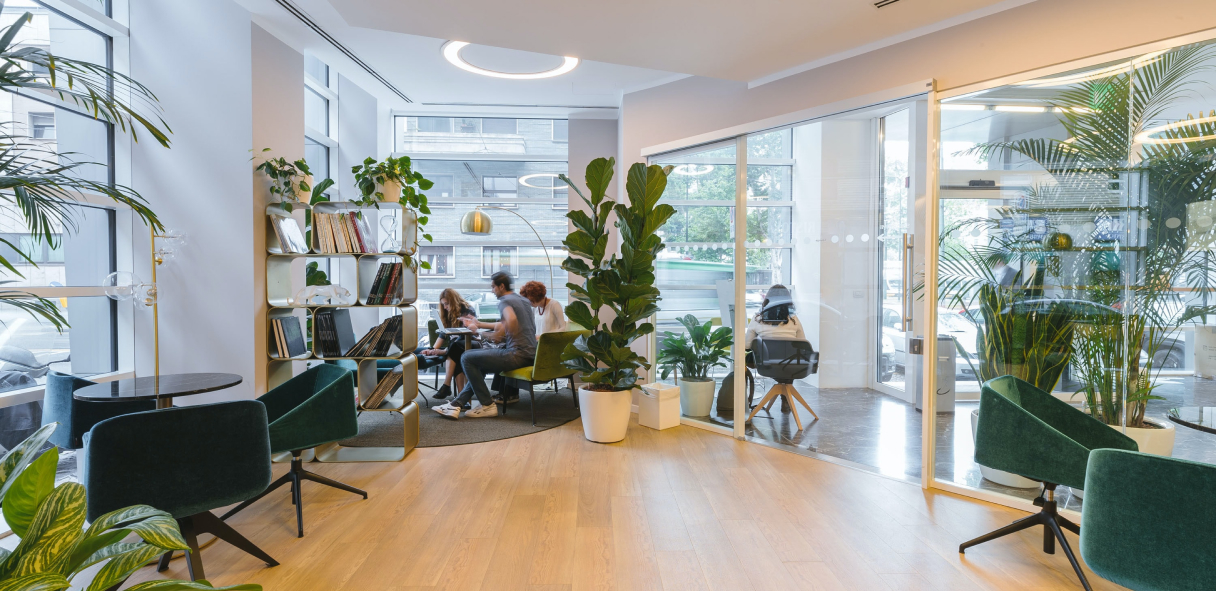
Introduction
In today’s global market, the demand for high-quality export furniture is growing rapidly. To meet international standards, furniture manufacturers must follow a strict and professional production process. This not only ensures product durability and aesthetics but also guarantees compliance with safety, environmental, and ethical regulations. Let’s explore the key stages of an internationally certified furniture production process.
1. Raw Material Selection
The journey begins with selecting premium-quality raw materials. Only sustainable and legally sourced woods, metals, fabrics, and finishes are used. Certifications like FSC (Forest Stewardship Council) are often required to prove the materials’ traceability and environmental responsibility.
Key standards applied:
- FSC, PEFC certification
- Moisture content control
- Grade-A wood and quality-tested hardware
2. Design and Product Development
Next comes the design phase. Product designers and engineers work together to create ergonomic, functional, and stylish furniture that meets market demands. 3D modeling and prototypes are tested for structural integrity, comfort, and user experience.
Key steps include:
- CAD drawing and prototyping
- Load testing and dimension checks
- Compliance with destination country regulations (e.g., ANSI/BIFMA, EN)
3. Cutting and Processing Materials
High-precision machinery like CNC routers and automated saws are used to cut and shape materials. This phase ensures accurate dimensions and efficient material usage.
International practices:
- CNC technology for accuracy
- Dust and waste control systems
- ISO-certified safety operations
4. Assembly and Joinery
Furniture components are assembled using strong joints like mortise and tenon, dowels, or metal fasteners. Skilled workers ensure structural stability and product durability.
Standards followed:
- Quality inspection during assembly
- Use of certified adhesives and fixings
- Alignment with ISO 9001 standards
5. Sanding, Finishing, and Coating
The surface treatment stage involves sanding, staining, painting, or coating. These steps enhance the product’s appearance and protect it against moisture, insects, and UV damage.
Eco-friendly practices:
- Use of non-toxic, lead-free paints
- VOC (Volatile Organic Compound) emission compliance
- UV-cured coating systems
6. Quality Control (QC) and Inspection
Every piece of furniture undergoes multiple quality checks before packaging. This includes mechanical testing, visual inspection, and performance evaluation.
QC checklist includes:
- Structural strength testing
- Surface finish inspection
- Packaging durability test (drop, vibration tests)
7. Packaging and Shipping
Products are packaged using international-grade materials like honeycomb cardboard, foam, and moisture-resistant wraps. Clear labels and assembly instructions are included to ensure smooth delivery and customer satisfaction.
Export readiness measures:
- ISPM 15-compliant pallets for international shipping
- Barcode and tracking system integration
- Optimization for container loading
Conclusion
Export furniture production is much more than just crafting beautiful products. It’s a systematic process that aligns with international standards, prioritizes sustainability, and ensures long-term customer satisfaction. By investing in a professional production process, manufacturers can confidently enter and thrive in competitive global markets.
- #design
- #wholesale furniture for projects
- #experiment
- #furniture supplier
- #trends
- #contract furniture manufacturer.
- #sofa
- #Acacia wood vs teak wood Best wood for export furniture Export furniture materials High-end teak wood furniture Affordable acacia wood furniture
- #tips
- #cushion
- #nguyen duc
- #funiture
- #furniture
- #indoor
- #outdoor
- #FSC
- #PEFC certification Moisture content control Grade-A wood and quality-tested hardware
- #What is OEM What is ODM OEM vs ODM in furniture Vietnam furniture export custom furniture manufacturing private label furniture
- #bulk furniture orders
- #fashion
- #optimize furniture costs
Lastest news
We would love
to hear from you !
Reach out to us via the form below or through our contact details, and we’ll get back to you as soon as possible.